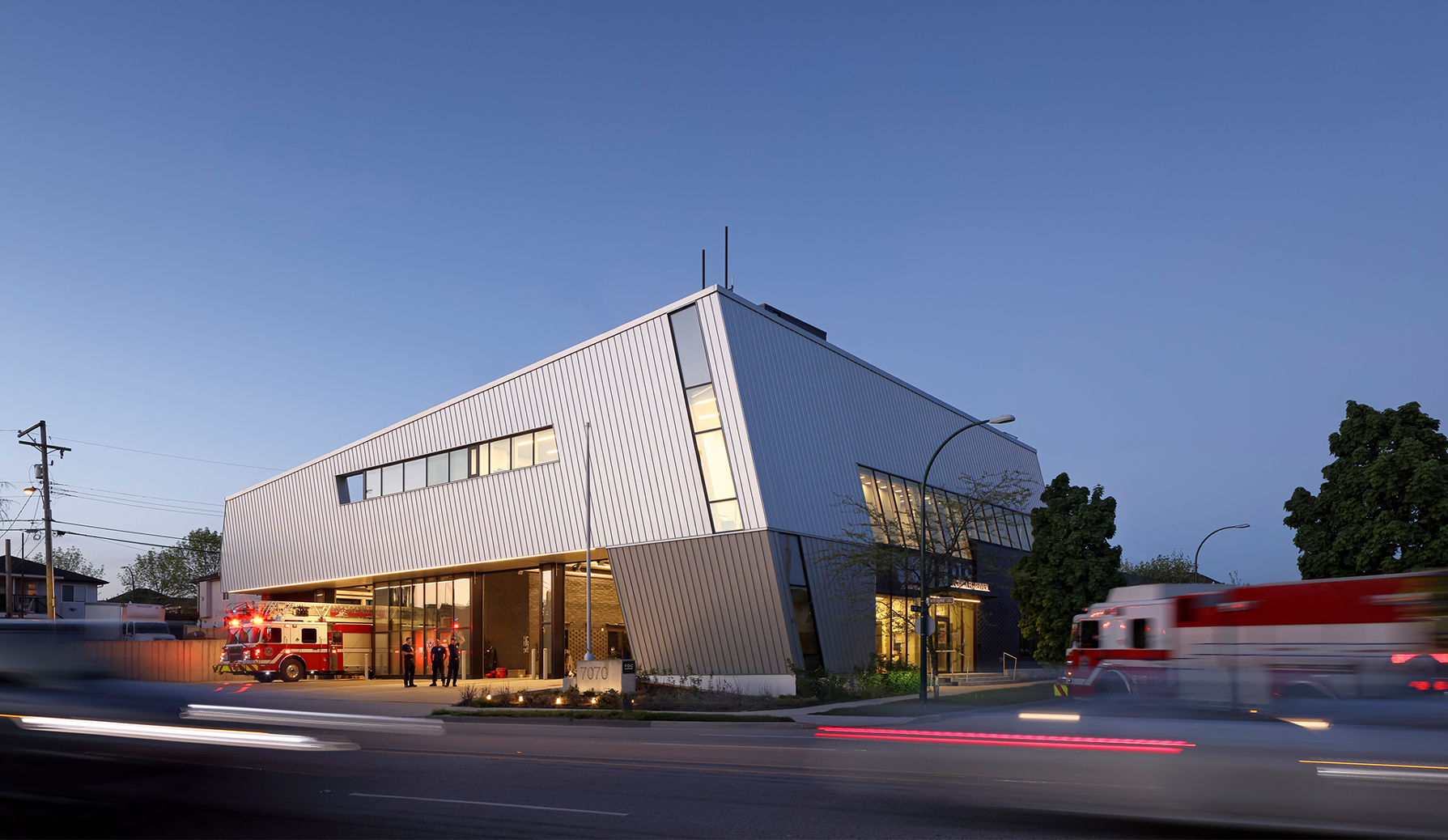
Vancouver Fire Hall 17
Location
Vancouver, BC
Vancouver Fire Hall 17 is North America's first Passive House certified fire hall. Aligned with Vancouver’s ambitious plan to achieve zero operational greenhouse gas emissions in new buildings by 2030, the redevelopment aims to meet the safety needs of the community both now and in the future.
The fire hall was the first in Canada to receive CaGBC Zero Carbon Building (ZCB) – Design certification, and is LEED v4 Gold certified. Design strategies include an airtight envelope, efficient air and water heat recovery systems, and a low carbon mechanical system that utilizes a geo-exchange field with ground source heat pumps. The design reduces greenhouse gas emissions by 99.7%, decreases energy demand, and enhances user comfort compared to its predecessor.
Disciplines
Areas of impact
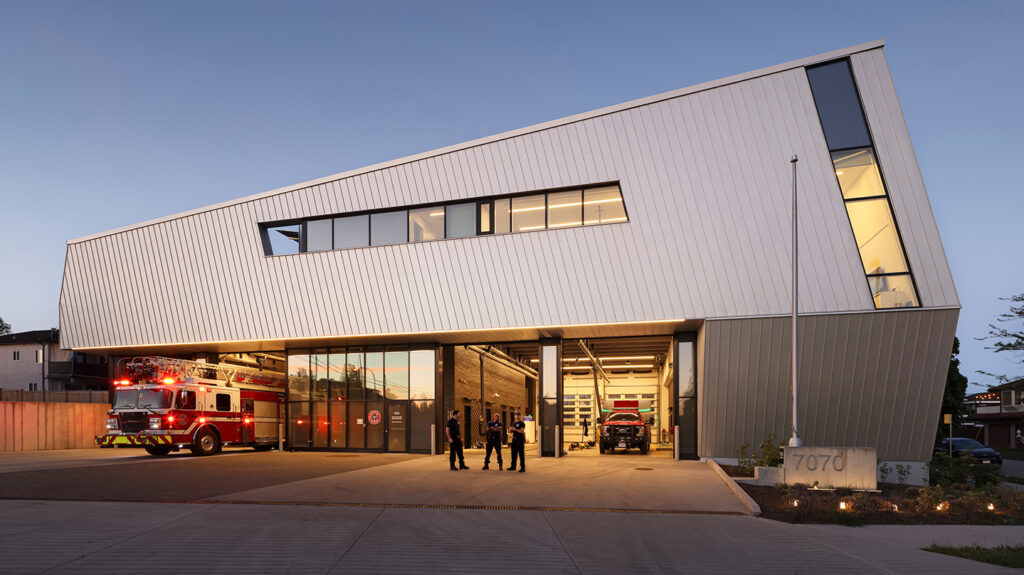
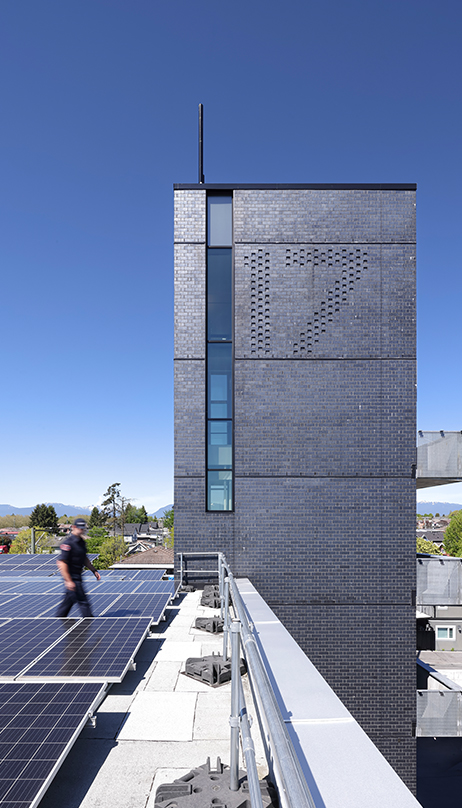
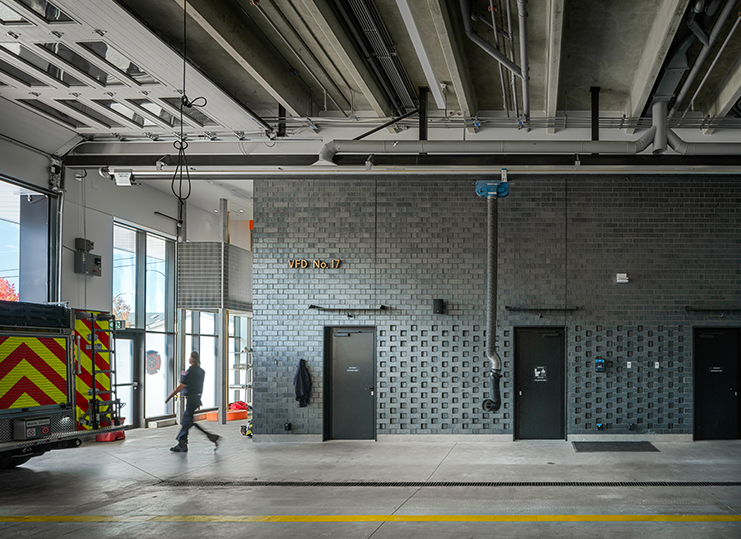
Putting first responders first
To accommodate modern firefighting needs and training, hcma collaborated closely with the City of Vancouver to design and construct the new fire hall. As Vancouver’s second largest training fire hall, the facility boasts four drive-through apparatus bays, a full-size hose/training tower, a training yard, and accommodations for a two-crew operation. Because the building is designed as a post-disaster facility, it's also fitted with IT, radio, SCADA (supervisory control and data acquisition), and traffic control equipment.
The safety, comfort, and wellbeing of firefighters were significant design drivers. Gender-neutral washrooms and single-occupancy dorm rooms facilitate privacy, the triple glazing and highly insulated envelope minimizes noise from the busy roadway, spaces exposed to contaminants have negative pressure to ensure containment, and multi-sensory alerting equipment maintain and support physical and mental health for staff.
The room used to store firefighter gear typically requires a very high air change rate to eliminate potentially harmful pollutants that could accumulate in the space. VOC sensors monitor the air quality in the space to assist in reducing ventilation rates and significantly lower energy consumption attributed to higher airflow rates.
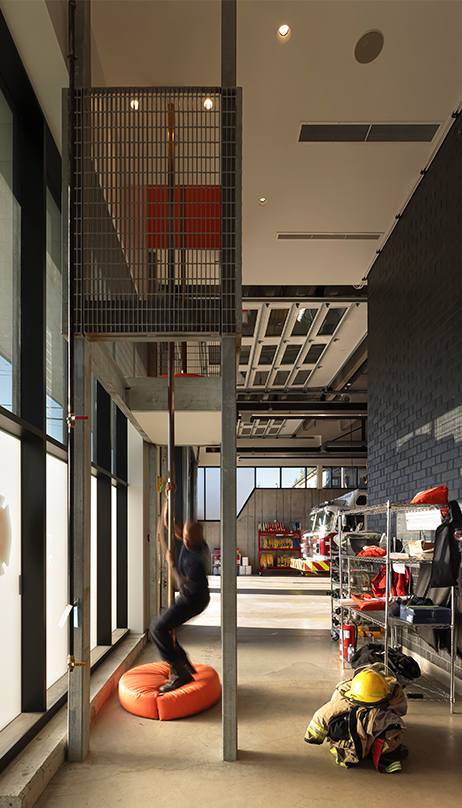
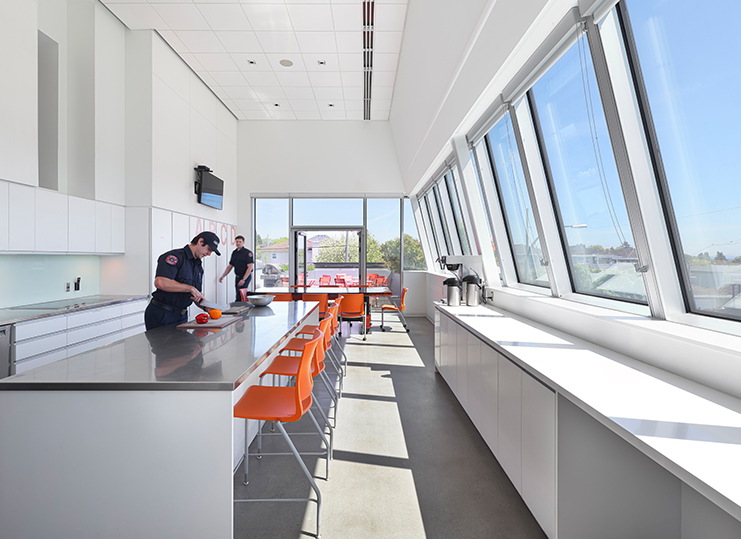
Design for a rapid response
Achieving quick turn-out time is the most critical design criterion in a fire hall. Turn-out time tracks the duration from notification of the call alarm, to disengagement from the task at hand, to physical movement towards the apparatus bays, to donning Personal Protection Equipment (PPE), and ultimately leaving the fire hall to attend the call.
Fire Hall 17 is designed so that any firefighter in the building can get to a fire truck in 60 seconds.
The firehall's interior features a white and neutral palette, with pops of orange and red to highlight exits and serve as intuitive wayfinding for firefighters. Clear, unobstructed hallways provide sightlines to corridor ends and outdoor views, helping orientation. Strategically placed windows and openings create transparency into key areas like the apparatus bays and kitchen. The fire poles are designed in a zig zag shape to facilitate a safer decent into the apparatus bays. The zig zag pattern is strategically designed to prevent injuries (broken ankles), which are common when landing on hard surfaces in high speeds.
In addition to following operational best practice, this criterion drove a compact and efficient massing with a low form factor. This “no cost” strategy considerably limits the thermal conductivity through the building envelope and the length of thermal bridges.
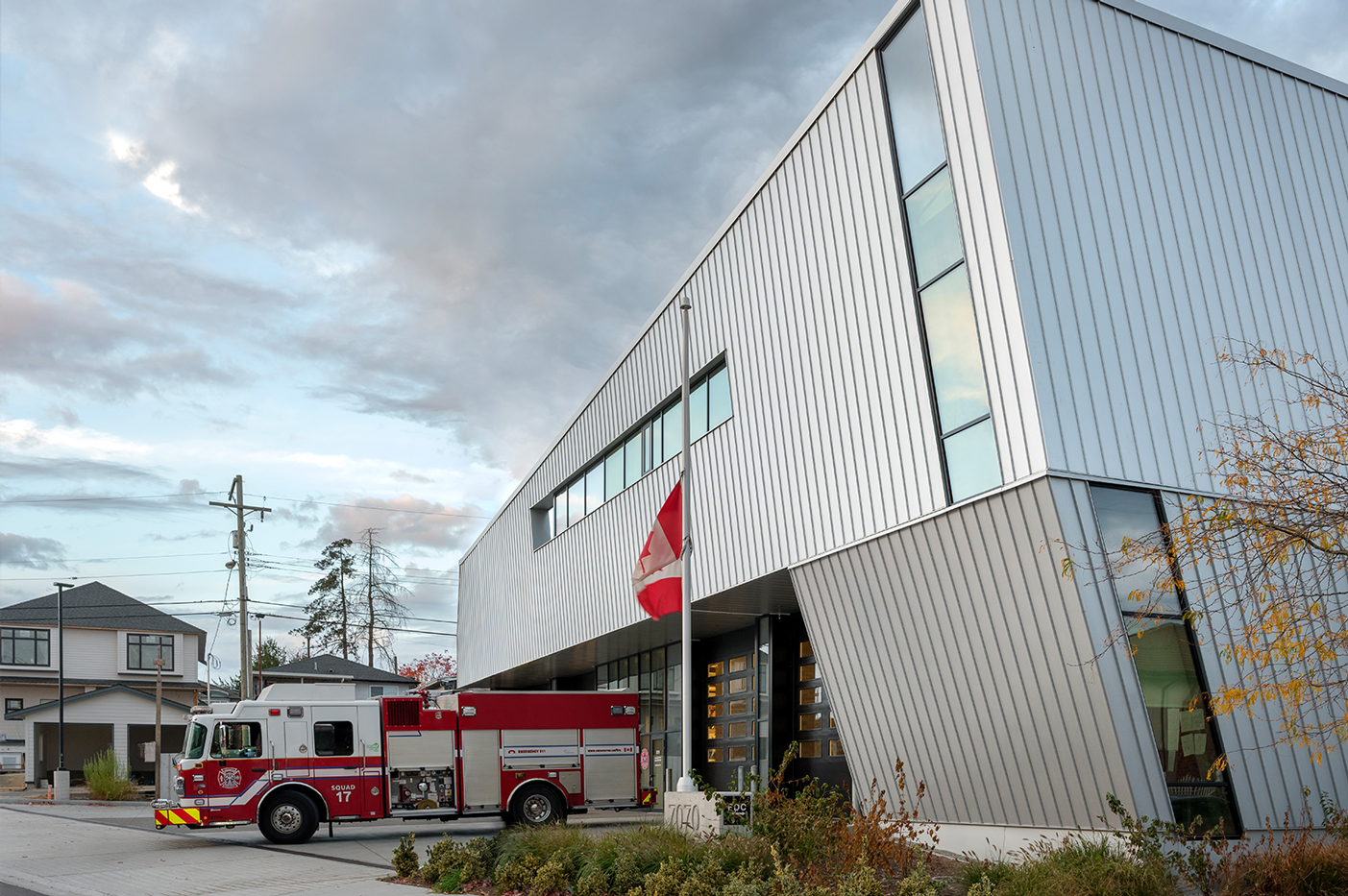
24 hours a day, 7 days a week
Achieving the stringent performance required by the three rating systems pursued by the project—ZCB, LEED Gold, and Passive House—was no easy feat, especially given the distinct operational requirements of the typology.
Fire halls operate 24 hours a day, 7 days a week. Not only must heating, cooling, lighting, and ventilation remain operational at all times, these loads are significant when considering the energy-intensive equipment on-site, including specialized IT and communication tools. In addition to energy-usage, the issue of airtightness—a fundamental Passive House design strategy—was complicated by having several apparatus bays with overhead doors.
To overcome these challenges, the design team defined two Passive House zones within the one facility. The administrative and living areas are conditioned at 20°C while the apparatus bays function at 10°C to maintain comfortable working conditions and prevent equipment from freezing. Certification of the 10°C area was ruled out due to the overhead doors but was modelled in a separate PHPP and fulfills all other Passive House criteria to guarantee the energy efficiency of the project as a whole. While the overall building massing is compact, the two zones feature complex geometries, increasing transmission heat losses. The boundary between the two zones required careful detailing, similar to an exterior wall condition, that included a continuous air barrier membrane and the identification of thermal bridges.
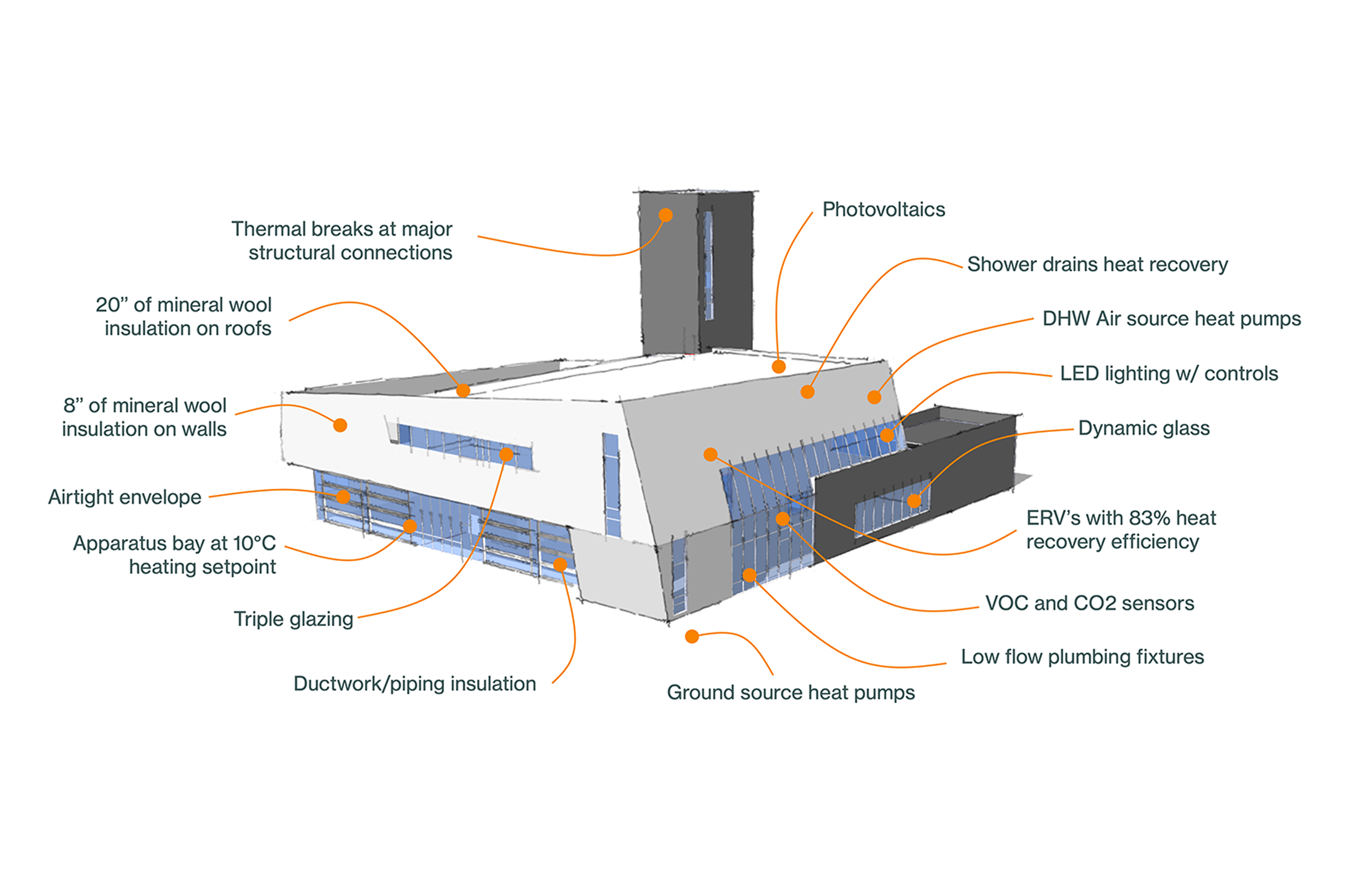
Other technical strategies
Electrochromatic glass is used on the East, West and South elevations as an effective and low maintenance strategy to shade and control glare while maintaining beneficial solar heat gains in the winter. The electronically tinted glass is integrated into the building automation system which ensures the cooling load is controlled passively before triggering the active cooling system. Because this solution relies on low voltage electricity, the energy consumption to operate the system is minimal, estimated at 172 kWh/y.
85.8 kW of photovoltaics have been installed on the roof, which are expected to generate 83,080 kWh of energy annually, off setting 100% of the building’s energy consumption, excluding process loads such as gear washing and IT equipment.
Three water-to-water heat pumps connected to a closed loop geoexchange field provide heating and cooling to the building. Twelve boreholes were required to meet the building’s annual heating and cooling demands, an additional three were installed for added resilience. A building designed to current minimum building code would have required 70 boreholes, at significant cost, and impossible to accommodate on this constrained site.
The fire hall is a city IT hub with both steady and significant loads. Although these loads contribute to a higher primary energy demand, the excess heat from the IT room is transferred via ductwork to the mechanical room where the domestic hot water heat pumps are located, providing free energy to pre-heat the hot water. This strategy also helps to minimize the cooling loads required for the IT room.
“The new Fire Hall 17 is a leading example of the City of Vancouver’s innovative approach to meeting climate commitments while investing in our city and providing the services Vancouverites depend on. It is a demonstration we can make near zero-emissions buildings the new normal, while also helping to reduce energy and water consumption costs.”
Ken Sim, Mayor, City of Vancouver
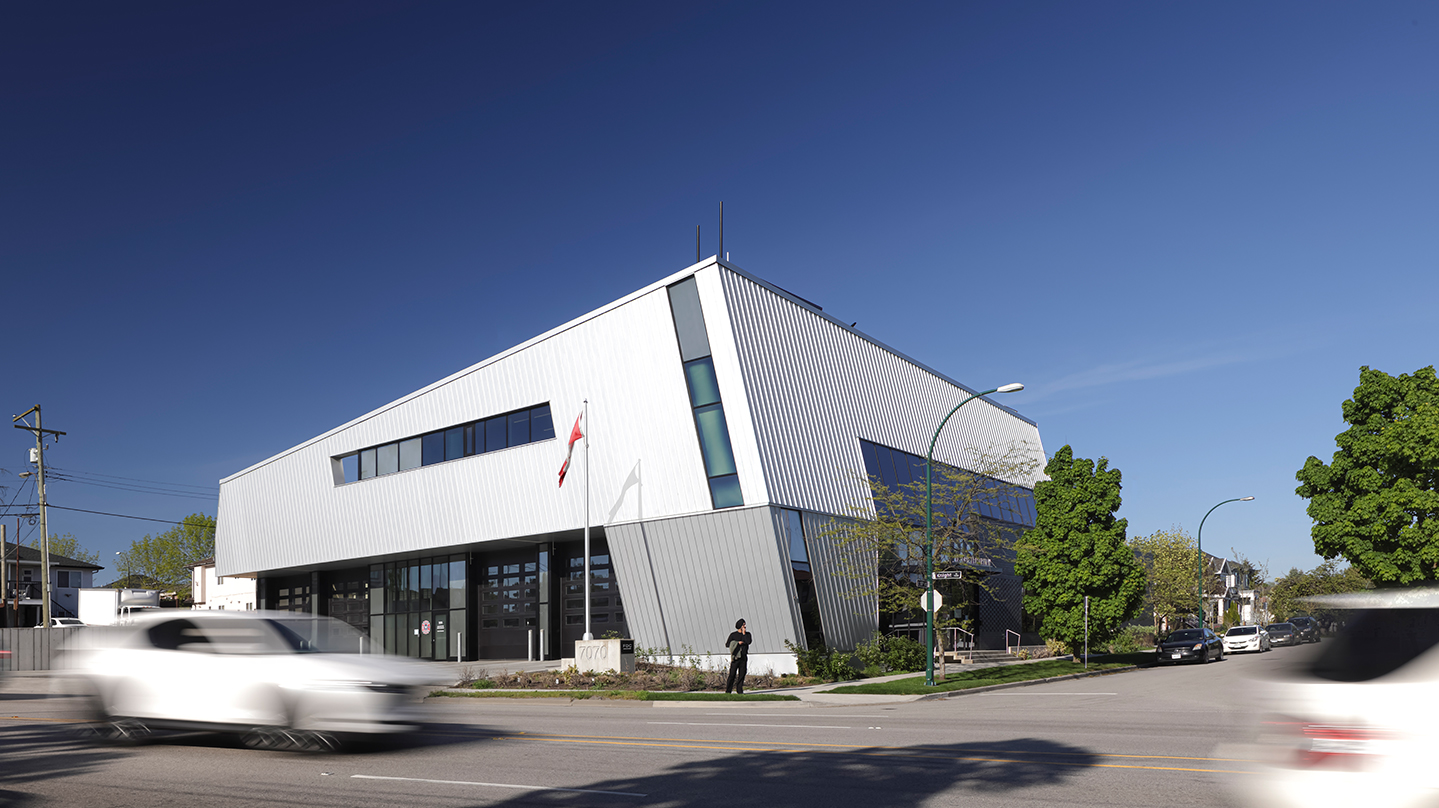
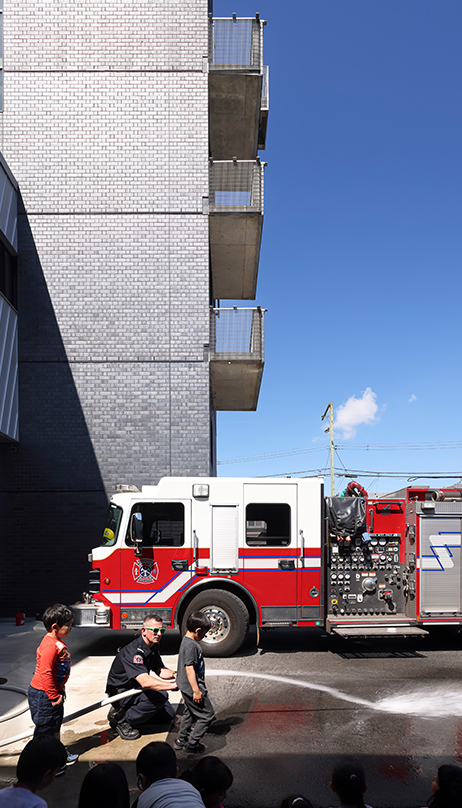
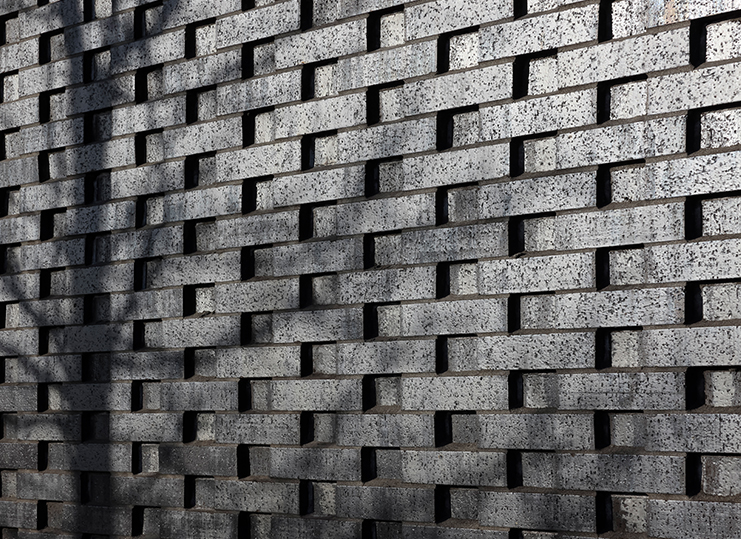
Read more on the project's sustainable design strategies in this case study from the Zero Emission Building Exchange (ZEBx).